Projeto de instalação para fabricação contínua de OSD
Por Allison Cacciatore, diretor executivo de design e engenharia de instalações, Pharmatech Associates
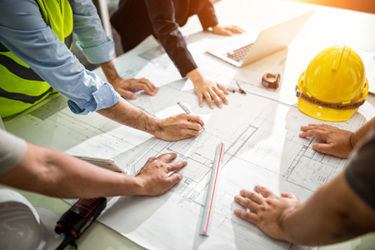
Várias formas de dosagem sólida oral (OSD) são bem adequadas para o processamento de fabricação contínua. Liberação em tempo real, área de instalação menor e custos de fabricação mais baixos a longo prazo são três fatores importantes que contribuem para a vantagem econômica do processamento contínuo em relação ao processamento em lote. A fabricação contínua é benéfica para empresas que buscam simplificar as operações de fabricação, mas nem todos os tipos de produtos OSD são bons candidatos. Este artigo considera os tipos de OSD a serem visados e compara a construção de novas instalações com a renovação.
O projeto de instalações para fabricação contínua de OSD difere significativamente do projeto de instalações dedicadas ao processamento em lote. As principais diferenças residem no layout da instalação, em termos de consolidação das operações da unidade, dimensionamento da utilidade e envolvimento limitado do processo manual, o que minimiza o número de pessoal necessário. A redução na complexidade das instalações, com menos salas para operações individuais, leva a menos pessoal necessário para realizar atividades de manutenção. Existem considerações específicas para redução de escala e velocidade de processamento. A redução de espaço proporciona menores gastos de capital e a redução de pessoal contribui para diminuir o custo operacional.
Pegada da instalação
O tamanho e a forma de uma instalação para fabricação contínua de produtos OSD fornecem um espaço menor e mais compacto do que o processamento em lote tradicional. No entanto, o tamanho e a forma dependem da tecnologia utilizada. Em alguns casos, principalmente para processamento de granulação úmida, o prédio precisa ser mais alto para acomodar o fluxo linear vertical do equipamento de fabricação contínua. Mas, em geral, a metragem quadrada geral é menor do que em uma instalação tradicional, pois as operações da unidade não são segregadas e não requerem conjuntos de processamento distintos. Em uma instalação tradicional, o espaço de preparo climatizado é necessário para as caixas que armazenam os materiais liberados entre as etapas do processo. Cada etapa requer amostragem, um registro de lote separado e liberação antes que possa avançar para o processamento. Com fabricação contínua,
Impacto da operação da unidade
Durante o processamento em lote, todas as operações unitárias são realizadas em salas diferentes. As etapas típicas incluem secagem, mistura, moagem, compressão e revestimento. Cada sala contém seus próprios operadores e controles de sala individuais.
Com a fabricação contínua, as operações unitárias não são mais segregadas. O ônus associado à manutenção da certificação de conjuntos distintos para monitoramento ambiental é minimizado e os procedimentos que regem o processamento tornam-se otimizados e simplificados. Durante a produção em lote, cada etapa do processo é gerenciada individualmente, mas com o processo de fabricação contínua, há um registro geral do lote e documentação associada em vez de muitos. Se a empresa estiver interessada em fornecer o API à dose sólida oral continuamente, ainda haverá a necessidade de liberar o API antes de iniciar o processo OSD. Isso afeta diretamente a velocidade do processo e historicamente não oferece nenhuma vantagem sobre o fornecimento em lote.
Redução de Escala e Velocidade de Processamento
Normalmente, existem três métodos para a produção de OSD: compactação por rolo, compressão direta e compressão úmida. A compactação do rolo pega o pó e o pressiona com força entre dois rolos pesados, produzindo uma fita frágil que se quebra em flocos que são então peneirados até que uma distribuição de tamanho de partícula desejada seja alcançada; essas partículas são então pressionadas juntas para fazer comprimidos. Com a compressão direta, o material é reunido através de vários alimentadores diferentes para o API e vários excipientes, alimentado a um misturador e enviado diretamente para as prensas da máquina de compressão para formar comprimidos. Compressão úmidacontém um conjunto de alimentadores que podem ser preenchidos manualmente ou retirados a vácuo dos tambores, transportados pneumaticamente para a tremonha alimentadora, depois alimentados em uma área de mistura e depois em um granulador de rosca dupla que produz os grânulos úmidos que são alimentados em um secador segmentado para uma unidade de tratamento que moe o produto no tamanho correto. Há uma etapa de mistura adicional, normalmente com estearato de magnésio, antes de ser alimentado na etapa de compressão.
Ao fabricar continuamente produtos OSD, a escolha mais fácil e econômica para o processamento é a compressão direta. Esse método é mais fácil porque fornece uma mistura contínua que lida melhor com a variação do material, facilitando o controle da variabilidade do produto. Na fase de desenvolvimento, mais experimentos são possíveis, tornando a seleção de compressão direta mais facilmente adaptada às necessidades do produto final.
Se a única opção para o produto for a granulação úmida, não há uma grande redução no custo realizado, pois esse processo se traduz em um processo totalmente vertical no formato de fabricação contínua. Normalmente, a instalação precisará ser muito alta (três a quatro andares) para acomodar o equipamento necessário. No entanto, se a granulação úmida for a única opção, um greenfield geralmente é mais barato do que renovar uma instalação existente que pode não ter a altura necessária ou estrutura de aço apropriada para suportar a adição de andares extras para acomodar o processo.
Impacto Pessoal
Com o processamento contínuo e a eliminação de operações unitárias discretas, a quantidade de supervisão do processo é reduzida. Além disso, a inclusão do PAT resulta em monitoramento automatizado em tempo real do processo que pode ocorrer virtualmente, com menos necessidade de supervisão humana.
As instalações de fabricação contínua são simplificadas em comparação com as instalações em lote. Há menos salas para operações individuais, levando a menos atividades de manutenção necessárias, o que minimiza o número de pessoal necessário do ponto de vista da manutenção.
Em geral, o custo associado ao treinamento de pessoal no processo de fabricação contínua é alto, pois esse conhecimento não é comum e o número de pessoal experiente é limitado.
Serviços de utilidade pública
HVAC
Com o contínuo, há uma necessidade reduzida de capacidade de HVAC, pois o processo é integrado e a necessidade de suítes separadas e câmaras de descompressão é praticamente eliminada. A necessidade de espaço de preparo climatizado para lotes também é eliminada. A redução de custos é realizada nas despesas de capital, bem como nos custos operacionais e de manutenção. A própria unidade pode ser muito menor devido ao tamanho reduzido do ambiente controlado e um projeto mais econômico que limita a necessidade de acesso do pessoal ao(s) conjunto(s) de produção.
Limpeza de equipamentos
Uma desvantagem da fabricação contínua é a quantidade de água e produtos químicos necessários para a limpeza do equipamento, que é mais complexa do que o processamento em lote e não se presta à limpeza no local (CIP). São necessárias desmontagens e manipulações manuais do equipamento para transportar as peças para outro local para limpeza. Dependendo da natureza do produto que está sendo processado, o tempo real de limpeza e troca será afetado. Se o processo de limpeza for extremamente longo, conjuntos extras de peças de reposição podem ser usados para manter o equipamento em operação, embora possam ser caros, pois esse equipamento é complexo e específico do produto. A tecnologia de uso único tornou-se predominante no processamento em lote, mas ainda não fez incursões significativas na fabricação contínua, embora os usuários finais estejam interessados nesta aplicação.
Outros Utilitários
O vapor não é usado para fabricação contínua. O ar quente é usado para secagem durante o processo de granulação úmida, mas é manuseado localmente e requer aquecimento. O nitrogênio pode criar problemas no sistema de alimentação se for usado como cobertor. A vibração do equipamento da máquina de compressão pode migrar para os alimentadores. Os alimentadores devem ser fixados à coluna de concreto da instalação para eliminar os harmônicos da vibração, que podem afetar negativamente as células de pesagem e afetar sua precisão.
Construir ou reformar?
A tabela a seguir compara e contrasta as vantagens da fabricação contínua em uma nova instalação construída desde o início (greenfield) com o mesmo tipo de operações em uma instalação e infraestrutura existentes adequadas (brownfield).
O caso da fabricação contínua
Resumindo, o custo-benefício da fabricação contínua é obtido por meio da facilidade de processamento, monitoramento contínuo e redução de operações manuais que contribuem para um processo simplificado e espaço reduzido em comparação com operações unitárias separadas. A fabricação dessa maneira resulta em custos operacionais mais baixos e menos perda de produto ao longo do processo de fabricação.
Sobre o autor:
Allison Cacciatore é diretora executiva de design e engenharia de instalações da Pharmatech Associates. Com mais de 15 anos de experiência em projeto de instalações, engenharia e gerenciamento de construção, ela liderou projetos multimilionários de renovação, desde a viabilidade e projeto conceitual até o licenciamento de instalações de vacinas biológicas e virais. Ela liderou a supervisão técnica na inicialização de uma linha de envase durante a pandemia de gripe de 2009. Experiência adicional inclui validação baseada em risco e ASTM E-2500, e ela foi consultora para a indústria de plásticos e produtos químicos especiais. Cacciatore possui MBA em administração e bacharelado em engenharia química pela Lehigh University.
Nenhum comentário:
Postar um comentário