Tecnologias de mistura recomendadas para a produção de invólucros de cápsulas
Por Christine Banaszek
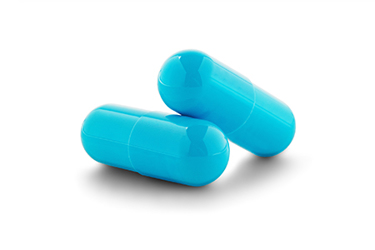
As químicas do invólucro da cápsula hoje devem atender a uma infinidade de requisitos, incluindo aqueles afetados pelas preferências do consumidor, a necessidade de compatibilidade com ingredientes farmacêuticos ativos, as taxas de dissolução e a sensibilidade à umidade de uma formulação, a permeabilidade aceitável ao oxigênio e a estabilidade geral do produto.
As mais comuns são as cápsulas de gelatina dura, tipicamente feitas de material de colágeno de origem animal. As opções vegetarianas incluem cápsulas feitas de hidroxipropilmetilcelulose (HPMC), amido de batata e pululano (tapioca). Agentes gelificantes secundários, como carragenina, goma gelana, pectina, ágar e goma xantana, também podem estar presentes. Os fornecedores de cápsulas também fabricam cápsulas de acetato de polivinila (PVAc) para preenchimento com medicamentos insolúveis em água que foram dissolvidos em solventes como polietilenoglicol (PEG).
Os invólucros das cápsulas são classificados em hard ou softgel, sendo este último plastificado pela adição de glicerina, sorbitol ou um poliol similar. Os fabricantes farmacêuticos podem encher cápsulas com pós, grânulos, pellets, líquidos, géis, pastas ou cápsulas menores. Com as propriedades químicas e físicas corretas, as cascas podem acomodar uma combinação de ingredientes incompatíveis em uma única cápsula.
Dadas as diferentes matérias-primas e requisitos de aplicação em jogo, você pode simplificar a seleção do misturador para uma formulação de cápsula-invólucro específica, considerando a viscosidade da formulação e o nível apropriado de cisalhamento. O perfil de viscosidade durante a mistura é função da própria formulação, mas outros fatores também a influenciam, como a ordem de adição dos ingredientes, a temperatura de processamento e a entrada de cisalhamento. Na maioria das vezes, a afinidade dos componentes secos com o veículo líquido com a facilidade com que os pós se dispersam ou se dissolvem determina a ação e a intensidade de mistura adequadas.
Misturador planetário duplo
Se o lote for consideravelmente espesso, denso e/ou pegajoso, um misturador planetário duplo (DPM) normalmente é a melhor escolha (foto). Sua velocidade relativamente baixa depende da alta viscosidade de uma formulação para transmitir cisalhamento à medida que suas duas lâminas idênticas giram em eixos individuais enquanto circulam o lote, empurrando o material contra as superfícies do recipiente e entre as lâminas. Quanto maior a viscosidade, maior o cisalhamento resultante da ação de amassar das lâminas do DPM, o que ajuda a suavizar a consistência e a separar os aglomerados soltos.
Certos géis de cápsula são sensíveis ao cisalhamento e um ajuste perfeito para as lâminas DPM de baixa velocidade, independentemente de a viscosidade permanecer relativamente fluida. Para ingredientes secos que são bastante fáceis de dispersar, com grumos facilmente desintegrando sob baixo cisalhamento, a ação de mistura suave e completa do DPM é ideal. Como vantagem adicional, você pode desaerar facilmente um lote puxando vácuo no DPM. Por outro lado, uma lâmina de alta velocidade às vezes pode micronizar o ar aprisionado no material, dificultando a remoção mesmo sob vácuo profundo, e você pode cisalhar demais o produto, o que pode levar a uma perda permanente de viscosidade.
Misturador multi-eixo
Um misturador de vários eixos é eficaz para formulações de cápsulas que exigem alto cisalhamento, mas não são extremamente viscosas. Géis lisos ou escorregadios geralmente são bons candidatos para processamento em um misturador de vários eixos, que compreende dois ou mais agitadores acionados independentemente trabalhando em conjunto. Uma âncora de baixa velocidade pode complementar um ou dois dispositivos de alto cisalhamento, como uma lâmina dispersora aberta estilo disco ou um conjunto rotor/estator.
Por si só, uma lâmina dispersora pode produzir padrões de fluxo aceitáveis em lotes de até cerca de 50.000 centipoises e o conjunto rotor/estator de até cerca de 10.000 centipoises. Para aplicações que excedem esses limites de viscosidade aproximados, é necessário um agitador de âncora para garantir fluxo em massa suficiente e entregar a formulação ao dispositivo de alto cisalhamento. A âncora é frequentemente equipada com raspadores para limpar a formulação das superfícies de um recipiente e otimizar a transferência de calor. As paredes laterais e o fundo de uma embarcação são normalmente encamisados para fins de aquecimento e resfriamento.
Para maior eficiência, você pode substituir o rotor/estator convencional em um misturador de vários eixos por um conjunto modificado projetado para indução de pó subterrâneo (foto). Esses sistemas oferecem uma maneira perfeita de introduzir sólidos diretamente na zona de alto cisalhamento para dispersão imediata. Essa técnica encurta o processo de mistura, evitando que os pós flutuem na superfície do lote ou formem grumos persistentes, chamados olhos de peixe. Também minimiza a poeira, um problema de processamento comum associado a pós leves.
Tal método de indução de sólidos é mais aplicável quando o veículo líquido está começando com uma viscosidade semelhante à da água ou muito baixa. O conjunto modificado projetado para indução de pó subterrâneo em um misturador de vários eixos não depende de uma bomba de vácuo externa, mas requer alto fluxo de líquido para gerar uma sucção poderosa para injeção de pó. Uma variação possível neste tipo de sistema é um misturador autônomo de alto cisalhamento para o processamento de formulações e intermediários de baixa viscosidade.
Misturador planetário híbrido
Se os requisitos de alta viscosidade e alto cisalhamento se aplicarem, a melhor solução é tipicamente um misturador planetário híbrido (foto), que combina a ação de mistura completa de um agitador planetário com o benefício adicional de um dispersor de alta velocidade. Tanto a lâmina planetária quanto o dispersor de alta velocidade giram em seus próprios eixos enquanto giram em torno de um eixo central. A lâmina planetária em órbita varre continuamente as superfícies da nave e transporta o material em direção ao dispersor. Isso ajuda a distribuir o calor resultante da lâmina dente de serra de giro rápido, mantendo a temperatura e a viscosidade uniformes em todo o lote em todos os momentos. A velocidade variável permite o controle preciso das taxas de cisalhamento para minimizar a degradação de quaisquer componentes sensíveis ao cisalhamento.
Nenhum comentário:
Postar um comentário