Enfrentando 3 desafios usando o sistema de controle de peso automático do Tablet Press
Por Fred A. Rowley
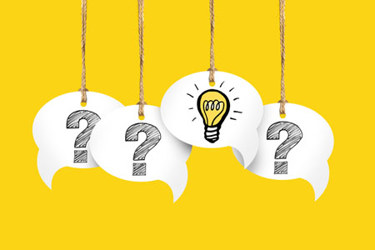
Em meu artigo recente publicado pela Outsourced Pharma e Pharmaceutical Online , apresentei informações sobre a operação de um sistema automático de controle de peso (AWC) fornecido por muitas empresas de fabricação de prensas como parte de uma moderna prensa de comprimidos. Depois que o AWC se tornou parte de uma prensa de comprimidos no final da década de 1970, ele rapidamente passou de um simples mecanismo de rejeição “sim/não” para parte do painel de controle central moderno.
Tornou-se objeto de preocupação por volta de 2009, quando uma infinidade de recalls de produtos para tablets grandes nos Estados Unidos desencadeou inúmeras investigações para determinar a causa raiz. Como resultado, várias das causas estabelecidas de comprimidos acima e abaixo do peso foram vinculadas ao AWC. Uma das causas principais foi a configuração incorreta dos limites de rejeição usados para eliminar os comprimidos fora da especificação de peso.
À medida que mais conhecimento se tornou disponível, identificando as causas comprovadas desse sério problema, a frequência de recalls diminuiu drasticamente e o problema foi considerado sob controle por quase uma década. Então, no início de 2022, ele reapareceu. Logo depois disso, vimos um item adicional adicionado à lista de verificação de inspeção e o início de uma fiscalização mais rígida por parte do FDA.
Para aqueles que não estão totalmente familiarizados com a operação AWC, o operador primeiro estabelece o peso-alvo especificado no registro do lote do produto e, em seguida, ajusta o controle de espessura para (espera-se) atingir a espessura-alvo do comprimido e, portanto, a espessura-alvo. O painel de controle exibirá uma pressão correspondente, chamada de “força de compressão”, que é a pressão usada para comprimir o comprimido em um volume de preenchimento específico de pó usando uma configuração de espessura de comprimido específica em uma velocidade de prensa específica.
Neste ponto, o operador é encarregado de definir dois “pontos de disparo” adicionais para os pesos mínimo e máximo permitidos dos comprimidos especificados no registro do lote. Este procedimento é frequentemente uma operação semi-manual em que o operador altera o volume de preenchimento (peso do comprimido) para cima ou para baixo para os pesos mínimo/máximo especificados. Novamente, podemos vincular esses preenchimentos (pesos) com as forças de compressão usadas para alcançá-los.
No registro do lote, os pesos de especificação mínimo/máximo geralmente estão em uma faixa de 5% em torno do alvo. Portanto, logicamente, as pressões de compressão mín/máx também devem ser 5% diretos em torno do alvo. E aqui reside o problema: o valor teórico muitas vezes não reflete a realidade. Sabendo disso, a FDA insiste que os pontos de ajuste de peso mínimo/máximo devem ser verificados para cada lote de cada produto para garantir melhor que todos os comprimidos defeituosos foram isolados do lote. Fazer isso é uma tarefa tediosa e demorada e, no entanto, deve ser realizada.
A prática atual da indústria para atingir esse objetivo não é padronizada. Algumas empresas tentam estabelecer esses pontos de ajuste fabricando um “lote de engenharia” e usando essas pressões de compressão únicas como configurações aceitas e comprovadas validadas para toda a produção futura. Outras empresas tentam usar valores teóricos calculados a seco na esperança de economizar tempo, esforço e produto. Finalmente, algumas empresas contam com o procedimento de configuração recomendado pelo fabricante da prensa de comprimidos, que quase sempre é baseado em um cálculo a seco.
Várias situações difíceis surgiram da reação da indústria e da adoção desse procedimento prolongado. Embora as empresas sejam obrigadas a absorver o custo do aumento da amostragem para atingir o peso alvo e os limites mínimo/máximo, além de tempos de inicialização atrasados e partidas abortadas mais frequentes por problemas técnicos, três problemas sérios surgiram:
1. Antes de definir os limites de rejeição de comprimidos, como posso verificar se a porta de rejeição está funcionando corretamente? Isso deve fazer parte do protocolo/SOP usado para verificar os limites de peso mínimo/máximo? Este foi um problema sério alguns anos atrás, quando vários recalls foram relacionados a comprimidos com excesso de peso que não foram detectados e removidos do lote durante a compressão do comprimido. Era um problema complexo e foi determinado que muitas das causas principais estavam ligadas à falha do mecanismo de rejeição em funcionar conforme necessário. A foto 1 é um exemplo do problema.
Foto 1: Tablet preso pelo mecanismo de rejeição
Como resultado, SOPs rigorosos e verificação mais frequente do portão de rejeição foram instituídos em todo o setor (espero que isso inclua sua empresa). Supondo que isso não seja um problema para você, agora estamos livres para abordar as duas preocupações restantes.
2. Em algumas situações, podemos encontrar amostragem inicial excessiva ao fabricar lotes pequenos. Como resultado, você pode exceder a perda máxima permitida e iniciar uma investigação obrigatória. Isso, por sua vez, também pode gerar algum tipo de plano de ação quando, na verdade, é desnecessário. E, além disso, há o custo do próprio produto que se perde.
Algumas empresas de medicamentos genéricos adotaram uma política recomendada por alguns fabricantes de prensas de comprimidos — selecionar valores mínimos/máximos de rejeição significativamente mais estreitos do que normalmente seriam usados como resultado de um teste de provocação. Observe os campos 10 e 11 na Foto 2 abaixo. Nesse caso, os resultados do teste de desafio foram 34,0 e 36,5, respectivamente, enquanto o ajuste final foi 25,0.
Foto 2
Essencialmente, estaríamos dispostos a aceitar uma perda maior de produto em troca de uma inicialização muito mais rápida e a correspondente economia de mão de obra.
3. Se eu estiver comprimindo um comprimido muito pequeno , digamos 50 mg, a diferença de pressão entre o peso alvo e os limites de peso mínimo/máximo declarados no registro do lote será muito pequena. Esse desafio é exacerbado se a prensa de comprimidos que estou usando tiver células de carga projetadas para comprimidos maiores. O resultado pode ser que estou rejeitando muito mais comprimidos do que o necessário porque o sistema de controle não é capaz de distinguir pequenas diferenças na pressão de compressão.
Tenho visto comunicações de empresas que adotaram a prática de usar os sinais gerados pela estação de pré-compressão, que possui células de carga projetadas para pressões muito menores, e “enganar” o sistema de controle fazendo-o pensar que isso representa as pressões reais usadas para fazer o comprimido. Uma abordagem mais profissional é solicitar que o fabricante da prensa de comprimidos forneça células de carga com capacidade para medir pressões muito menores.
Em conclusão, há várias situações que exigem que seu departamento de validação considere abordagens alternativas para desafiar a capacidade do AWC de identificar e remover comprimidos fora de especificação na fabricação de comprimidos genéricos comerciais. A aplicação cuidadosa dos procedimentos que discuti ajudará a atingir esse objetivo.
Sobre o autor:
Fred A. Rowley tem mais de 40 anos de experiência nas indústrias de suplementos farmacêuticos e nutricionais em manufatura, serviços técnicos e ambientes de P&D, com especial especialização em fabricação e treinamento de dosagens sólidas. Ele tem conhecimento dos processos de granulação, mistura, compressão de comprimidos e revestimento de filme para mais de 800 substâncias farmacêuticas API. Ele é e tem sido considerado um especialista no assunto por escritórios de advocacia, fabricantes de equipamentos, empresas farmacêuticas e de suplementos nutricionais internacionais e farmácias de manipulação, e lecionou no FDA, no ISPE e em muitas faculdades de farmácia em todo o mundo. Anteriormente, ele foi diretor de suporte técnico de fabricação da Watson Laboratories; gerente de fábrica, comprimidos e cápsulas, Weider Nutrition International; vice-presidente, operações, Arnet Pharmaceuticals; gerente de operações OROS, Alza Corporation; e gerente de sólidos a granel, Syntex FP, Porto Rico.
Nenhum comentário:
Postar um comentário