Os excipientes adquiridos de fornecedores diferentes se comportam da mesma maneira?
O Mixer Torque Rheometer pode ser usado para avaliar o comportamento de excipientes adquiridos de diferentes fornecedores.
fundo
Excipientes de diferentes lotes ou fornecedores podem variar em qualidade e muitas vezes é necessário realizar uma avaliação de pré-formulação para cada lote de excipiente recebido. Em alguns casos, os excipientes de diferentes fornecedores exigem uma avaliação comparativa de sua funcionalidade equivalente. Neste tipo de avaliação, o Mixer Torque Rheometer pode ser uma ferramenta inestimável para avaliar o desempenho potencial dos excipientes recebidos, em particular para auxiliares de esferonização.
Fig 1. Exemplo de curva MTR mostrando a relação entre o torque médio da massa úmida com adição de líquido umedecedor e quatro fases de interação líquido-sólido
Introdução
Os pellets são comumente produzidos por extrusão e esferonização. A celulose microcristalina (MCC) e a polivinilpirrolidona reticulada (XPVP) têm sido relatados como auxiliares de esferonização muito bons [1]. Para os dois excipientes, muitas marcas e qualidades estão disponíveis comercialmente. Diferentes empresas geralmente usam matérias-primas de diferentes fontes e empregam diferentes técnicas de processamento ou condições para fabricar seus excipientes. Mesmo com o mesmo processo e matérias-primas, existirá variabilidade de lote para lote. Portanto, as variabilidades em diferentes graus e lotes do mesmo excipiente são inevitáveis.
O MTR pode ser uma ferramenta de pré-formulação útil para caracterizar excipientes, em particular auxiliares de esferonização e classificá-los em vários grupos de acordo com seu desempenho na produção de pellets. Para o processo de extrusão-esferonização, a adição de água a uma mistura de pó para produzir uma massa úmida é necessária de modo a produzir uma massa de pó que seja suficientemente coesa. O MTR pode ser usado para caracterizar essa coesão, determinando o comportamento reológico da massa úmida [2].
Como o MTR envolve adicionar líquido à mistura de pó e misturá-los usando lâminas rotativas, a coesividade da mistura de pó estará relacionada à resistência nas lâminas de mistura e o torque resultante é medido e registrado. Os valores de torque são usados para descrever quantitativamente essa coesão. Com base neste princípio, uma curva mostrando a relação entre o torque médio e a adição de líquido pode ser gerada. Outro parâmetro, energia cumulativa de mistura, que descreve a entrada de energia total, também foi usado para avaliar o efeito das variações de grau do MCC na coesão e no comportamento reológico da massa úmida.
Estudo de Caso 1
Soh et al. avaliaram onze graus diferentes de MCC, coletados de diferentes empresas de excipientes em seu estudo [3]. A lactose também foi usada no estudo, uma vez que as misturas de MCC-lactose são comumente usadas para produzir pellets. O torque máximo de MCC [Torquemax (MCC)], torque máximo de mistura [Torquemax (mistura)], energia cumulativa de mistura de MCC [CEM (MCC)] e energia cumulativa de mistura de misturas [CEM (mistura)] foram medidos. O conteúdo de água usado variou de 75% - 175% (p / p) para MCC e 25-55% (p / p) para misturas. Os peletes foram produzidos usando misturas 3: 7 de MCC: lactose e 25, 30, 35, 40 e 45% (p / p) de água.
As propriedades reológicas medidas (parâmetros de torque) foram ainda correlacionadas com os graus de MCC e seus respectivos pellets.
O estudo foi fundamental para entender as características das partículas de MCC considerando sua saturação de líquido. Por exemplo, em menores quantidades de água usada, MCCs menos porosos, mais densos e mais cristalinos resultaram em torques maiores e, portanto, mais energia foi necessária para a mistura. Além disso, foram encontradas boas correlações entre as propriedades reológicas dos MCCs e MCC: misturas de lactose com as propriedades dos pellets produzidos, particularmente aqueles produzidos a 30 e 35% (p / p) de água.
Bacia e lâminas do reômetro de torque do misturador
Foi facilmente identificado que as propriedades físicas dos pellets preparados por MCC: blends de lactose podem ser comparadas com as propriedades reológicas dos graus de MCC e não foi necessário caracterizar a mistura binária. Assim, sem a necessidade de preparar a mistura de MCC: lactose para caracterização reológica, o tempo de análise poderia ser economizado na fase de análise de pré-formulação. Foi ainda identificado que as propriedades reológicas caracterizadas pelo MTR podem representar o grau de MCC de forma mais abrangente do que qualquer parâmetro de caracterização física único de MCC.
O estudo provou que o MTR pode ser uma ferramenta de pré-formulação poderosa para caracterizar auxiliares de esferonização e predizer as propriedades dos pellets a serem fabricados por extrusão-esferonização.
Estudo de Caso 2
Outro estudo, caracterizando diferentes graus de MCC usando MTR, confirmou ainda mais sua adequação como uma ferramenta de pré-formulação [4]. As propriedades reológicas de diferentes graus de MCC foram estudadas e o valor de torque médio foi usado para comparação de diferentes graus de MCC. Dois graus padrão de MCC com distribuição de tamanho de partícula semelhante foram obtidos de duas fontes diferentes e comparados.
Na maioria das vezes, os valores médios de torque foram menores para o MCC obtido de uma fonte do que para o MCC obtido de outra fonte. Essas diferenças nos valores médios de torque sugerem diferenças potenciais nas interações MCC-água, que podem impactar a qualidade do produto final do pellet. Assim, o desempenho do MCC obtido de diferentes fontes pode ser avaliado com base na caracterização reológica por meio de um reômetro de torque misturador.
CONCLUSÕES
- A energia cumulativa da mistura, um parâmetro de torque medido pelo Mixer Torque Rheometer, classificou os excipientes em grupos por seu desempenho previsto.
- A qualidade dos pellets produzidos usando diferentes graus de MCC pode ser prevista usando os valores de torque medidos.
- O valor médio do torque mostrou ser outro parâmetro importante para avaliar as funcionalidades e o desempenho dos auxiliares de esferonização.
REFERÊNCIAS
[1] Sarkar S, Heng PWS, Liew CV. Insights sobre a funcionalidade do auxílio da peletização na peletização por extrusão-esferonização. Pharm Dev Technol 2013; 18 (1): 61-72.
[2] Hancock BC, York P, Rowe RC, et al. Caracterização de massas úmidas usando um reômetro de torque misturador: 1. Efeito da geometria do instrumento. Int J Pharm 1991; 76 (3): 239-45.
[3] Soh JLP, Liew CV, Heng PWS. Parâmetros reológicos de torque para prever a qualidade do pellet em extrusão-esferonização. Int J Pharm 2006; 315 (1-2): 99-109.
[4] Luukkonen P, Schæfer T, Hellén L, et al. Caracterização reológica de massas úmidas de celulose microcristalina e celulose microcristalina silicificada usando um reômetro de torque misturador. Int J Pharm 1999; 188 (2): 181-92.
Ver 00129
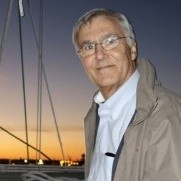
6 de agosto de 2020, em Mixer Torque Rheometer Application Notes , Mixer Torque Rheometer , MTR